top of page
Effettuare questo ulteriore esercizio è stato necessario a seguito di una stampa 3d non soddisfacente.
L'ingranaggio in questione non presentava la giusta precisione nella parte terminale dei denti; si è quindi optato per realizzare lo stesso pezzo in plexiglass, per sfruttare la precisione del taglio laser.
Il 2d originale è stato quindi rielaborato per posizionare al centro il foro esagonale per il posizionamento sul meccanismo.
Per il taglio è stato utilizzato il seguente parametro:
taglio passante > P100 V0.30
Sono stati tagliati più ingranaggi perchè lo spessore del plexiglass è di 3 mm mentre l'altezza dell'ingranaggio originale era di 15 mm.
Gli ingranaggi confrontati con il pezzo originale.
Il risultato è sicuramente più preciso e meno sbavato rispetto al pezzo stampato in 3d. L'altezza e lo spessore del vecchio componente, sono stati colmati impilando più ingranaggi in plexiglass, andando così a commarne gli spessori.
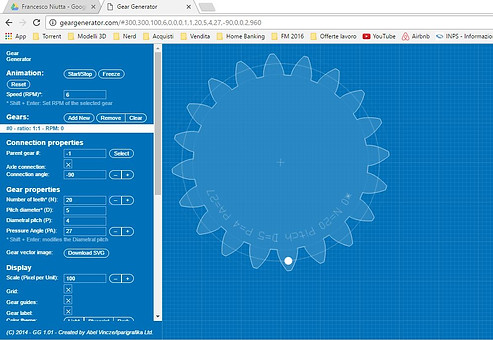
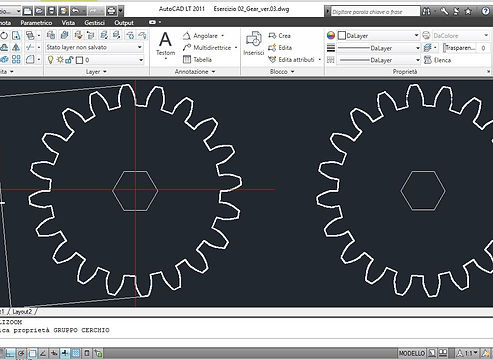



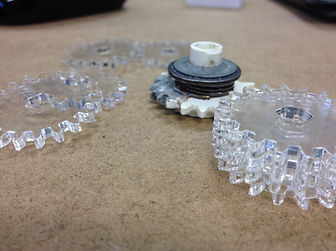


Una volta apllicati sul meccanismo originale però gli ingranaggi hanno presentato un problema considerevole: il foro esagonale era leggermente più largo del perno permettendo lo slittamento dell' ingranaggio stesso.
in fase di disegno infatti non era stato considerato il "kerf"; in pratica il laser tagliando consuma parte del materiale, aumentando le dimensioni del foro.
Sono quindi stati preparati altri ingranaggi in serie da tre, stringendo man mano il foro di un decimo di millimetro; sono inoltre stati aggiunti dei distanziatori circolari per facilitarne la rotazione.
Ogni serie è stata contraddistinta con un taglio non passante che riportava le dimensioni del foro.

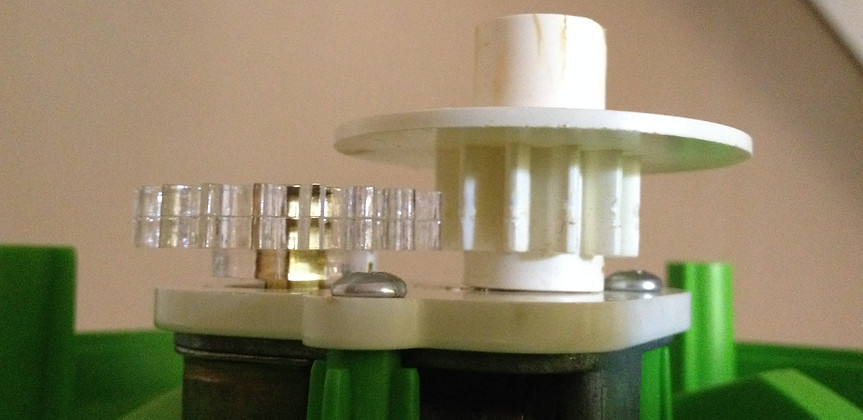
Il nuovo ingranaggio col foro da 7mm si applicava perfettamente sul perno, lavorando bene con quello che rimaneva del vecchio meccanismo.
Il carillion aveva ripreso vita!
Nella foto frontale, riportata in basso, si può notare la funzione del distanziatore circolare, il quale permette ai due ingranaggi di esseere perfettamente allineati.

05
ingranaggio in plexiglass
bottom of page